Lustron Homes of Sioux Falls
Multiple locations around town.
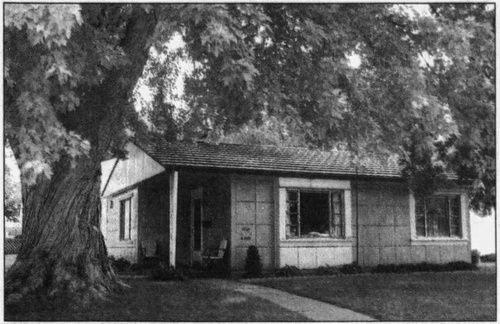
A 2-bedroom Westchester model built on Covell Avenue in 1950.
At the end of World War II the United States stood at a crossroads. Behind it, the scars of the war and the great depression ran deep, before it, the opportunity for prosperity or renewed peril. Part of the issue was the need for housing for the millions of soldiers returning from the war and their families. There were very few houses built during the great depression, and during the war, there were building restrictions to allow more materials to be directed to the war effort.
President Truman was of the opinion that the wartime assembly lines could be repurposed to build prefabricated homes for low-income households. Enter Carl Strandlund, a clever engineer hired by the Chicago Vitreous Enamel Product Company in 1942 to convert their factories to wartime production. Strandlund improved the efficiency and quality of defense production so much that he was promoted to vice president and general manager of the company in 1943.
In 1946 he went to Washington DC in hopes of getting a steel allocation from the government to build gas stations. The government had controlled steel during the war and still did for a time. Strandlund was given the cold shoulder on his gas station idea, but noticed that the feds were very interested in housing. Strandlund altered his idea from mass-produced gas stations to mass-produced homes. The federal Reconstruction Finance Corporation liked the idea and gave him a $15.5 million loan to get started. This was the birth of the Lustron Home.
President Truman was of the opinion that the wartime assembly lines could be repurposed to build prefabricated homes for low-income households. Enter Carl Strandlund, a clever engineer hired by the Chicago Vitreous Enamel Product Company in 1942 to convert their factories to wartime production. Strandlund improved the efficiency and quality of defense production so much that he was promoted to vice president and general manager of the company in 1943.
In 1946 he went to Washington DC in hopes of getting a steel allocation from the government to build gas stations. The government had controlled steel during the war and still did for a time. Strandlund was given the cold shoulder on his gas station idea, but noticed that the feds were very interested in housing. Strandlund altered his idea from mass-produced gas stations to mass-produced homes. The federal Reconstruction Finance Corporation liked the idea and gave him a $15.5 million loan to get started. This was the birth of the Lustron Home.
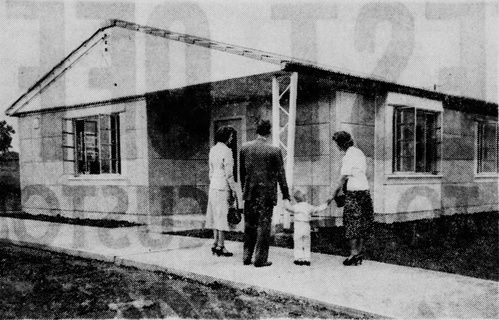
Young Jimmy Flynn sees his new home, the first one built in South Dakota at 1505 S. West Avenue. The Lewis Flynn family would soon move from Minneapolis to their new home in Sioux Falls. It's August 1949.
A Lustron home was a 2-3 bedroom home made of porcelain-coated steel panels. The Lustron home would have no wood to rot or be eaten by rodents or insects. It was designed to be fire-proof, lightning-proof, and maintenance-free. While one’s neighbors would have to paint and re-shingle every so often, the Lustron owner could sit on the small built-in porch after hosing down enameled steel panels for fifteen minutes, and sip iced tea or cosmopolitans.
The interior of a Lustron was similar to the exterior. All of the walls were porcelain-enamel coated steel panels. Built-in closets, bookshelves and vanities would make efficient use of the available inside space. The furnace would be kept out of the way in the attic space and many of them did not even include forced-air vents. Radiant heat would waft down from the ceiling panels in each room.
The construction of a Lustron home was just as amazing; All 3,000 parts would be produced in a 107 acre factory in Ohio, put on a truck and delivered to the assembly location. Two weeks later a house would emerge from the collection of enameled steel panels and assorted parts. It was not quite as easy as a Lego kit, but not too dissimilar.
The interior of a Lustron was similar to the exterior. All of the walls were porcelain-enamel coated steel panels. Built-in closets, bookshelves and vanities would make efficient use of the available inside space. The furnace would be kept out of the way in the attic space and many of them did not even include forced-air vents. Radiant heat would waft down from the ceiling panels in each room.
The construction of a Lustron home was just as amazing; All 3,000 parts would be produced in a 107 acre factory in Ohio, put on a truck and delivered to the assembly location. Two weeks later a house would emerge from the collection of enameled steel panels and assorted parts. It was not quite as easy as a Lego kit, but not too dissimilar.
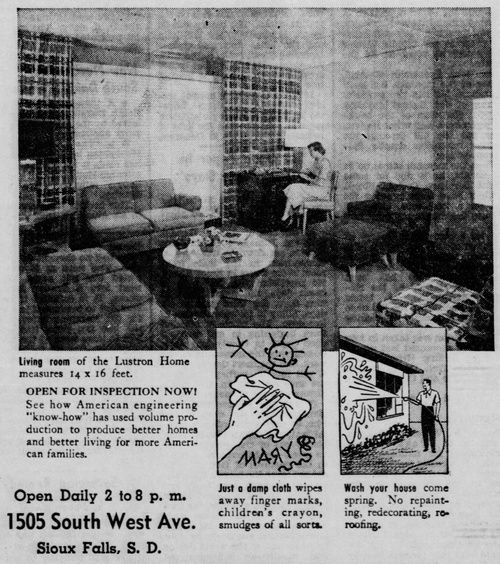
The Flynn's future home, shown above was used as a demo home for a while before the Flynns moved in. The furnishings were provided by Johnson Furniture.
Strandlund’s plan was to produce 100-150 homes per day, a goal he never met. Only 2,298 Lustron homes were produced between 1948 and 1950. Production problems and higher than projected customer costs hurt the Lustron company. When the government refused to loan more money, Lustron filed for bankruptcy and died.
Of the 38 Lustron homes constructed in the state, nine were in Sioux Falls. Of those nine, eight are still in existence. Most are two-bedroom Westchester models, though two are three-bedroom variations of the same model. One has a Lustron garage made from the same enameled steel panels. All Lustron homes in Minnehaha County were built by Leader’s Construction, who owned the local Lustron franchise. This franchise gave Leader’s a territory consisting of a 150 mile radius of of Sioux Falls. There were other contractors in Huron, Mitchell, Mobridge, Rapid City, and Watertown.
Of the 38 Lustron homes constructed in the state, nine were in Sioux Falls. Of those nine, eight are still in existence. Most are two-bedroom Westchester models, though two are three-bedroom variations of the same model. One has a Lustron garage made from the same enameled steel panels. All Lustron homes in Minnehaha County were built by Leader’s Construction, who owned the local Lustron franchise. This franchise gave Leader’s a territory consisting of a 150 mile radius of of Sioux Falls. There were other contractors in Huron, Mitchell, Mobridge, Rapid City, and Watertown.